In very basic terms, the reason that the shaft of any motor rotates (
when the motor is switched on) can be explained by one law of
Electromagnetic theory.
Fleming's Right Hand Rule.
This states that if an electric current is passed through a conductor
which is positioned perpendicular to the direction of a magnetic field, then
that conductor will experience a mechanical force tending to cause it to
move in a direction that is perpendicular to both the current flowing
through the conductor AND the direction of the magnetic field. The relative
directions of these three vectors can be deduced by holding one's right hand
with the thumb, first finger and second finger all perpendicular to each
other.
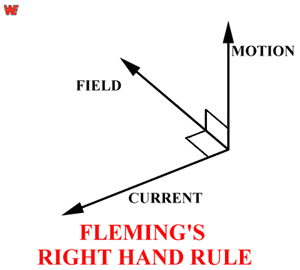
then: If CURRENT flows along the SECOND finger and the
FIELD flows along the FIRST finger then the resultant MOTION
will be in the direction of the THUMB.
In a typical A.C. Electric Motor, a rotating magnetic field is set up by
the current flowing through windings in the stator. This current also causes
an "induced" current to flow through the bars in the rotor (hence the term
"induction" motor). The resultant force causes the rotor to rotate as it
continually "chases" the rotating magnetic field and , since the rotor is
firmly fixed to the shaft, the shaft also rotates.
General Arrangement and Parts List
Motor 1D80-132 Frames
Parts Description
- Endshield D.E. with Oil Seal.
- Wave washer
- Bearing D.E.
- Terminal Box.
- Terminal Box Lid.
- Stator Lamination Pack.
- Rotor Lamination Pack.
- Stator Frame.
- External Earth Stud.
- Endshield N.D.E. with oil seal.
- Bearing N.D.E.
- Fan Cowl.
- Fan.
|
Specification
- Cast Iron Frame, Endshields.
- Aluminium Terminal Box.
- Pressed Steel Cowl.
- Endshields with Oil Seals.
- Polypropylene Fan.
- SKF or equivalent Bearings.
Features
- Dimensions and Ratings to IEC 72, AS 1359, BS 4999.
- IP55.
- Top Mounted Terminal Box.
- Terminal Box Rotates in 90 deg. increments.
- Drilled and Tapped Hole in D.E. of Shaft
- Cooling IC 0141
Mounting
- B3 - Foot Mounted
- B5 - Flange Mounted - Horizontal
- B3 / B5 Foot and Flange Mounted
- V1 - Flanged Mounted - Vertical
|
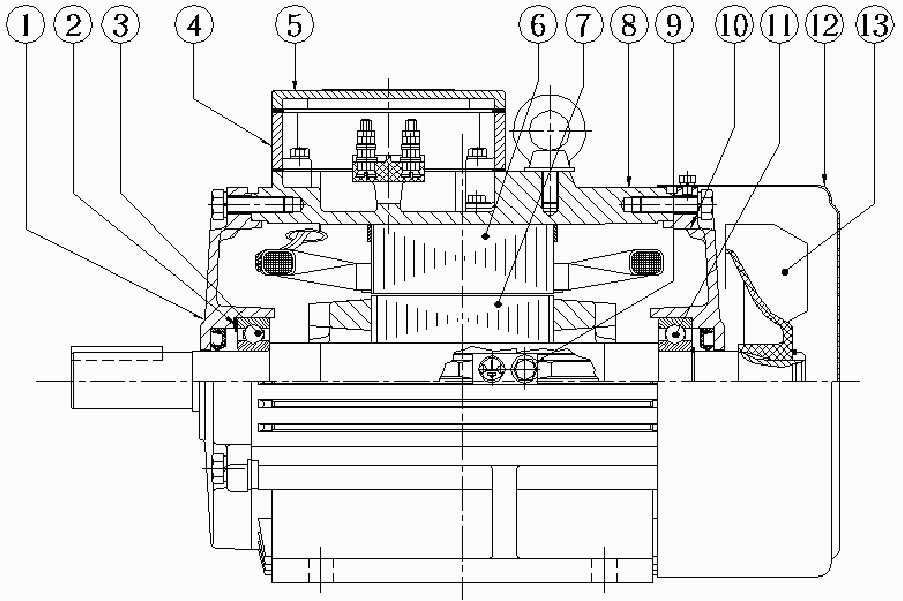 |
The basic construction of A.C. Induction motors has changed very little
over the years and we will now discuss some basic items.
The windings in a motor are there to provide a path for the A.C. current
to flow which in turn produces the magnetic field which will cause the rotor
to rotate.
The windings are insulated copper wire and inserted into slots in the stator
laminations. These slots have insulation between the windings and the steel
laminations. This is known as the "stator pack". The windings are designed
to provide the output and speed required.
The stator pack is, in turn, inserted into the motor casing known as the
"stator frame". The ends of the winding are brought out through the motor
casing to terminals in a terminal box mounted on the frame. This is where
the mains leads are connected.
This consists of laminations, shaft, bearings and a "winding".
The type of "winding" will depend on the type of motor required.
If the rotor has a winding similar to that of the stator it is known as a
"wound rotor motor". The wound rotor motor also is provided with copper or
brass rings on the shaft and brushes. These transfer the current generated
in the rotor to external resistance banks used to bring the motor up to
speed or control the speed. When the motor is up to the full load speed the
slip rings are shorted together to enable the motor to run continuously at
the full load speed.
If the "winding" consists of solid bars, that are joined either end by a
shorting ring, it is known as a "squirrel cage rotor" motor. This is because
the cage of the rotor resembles the cage that squirrels use to play with
when in captivity. The bars are generally aluminium but can be copper or any
such material. The squirrel cage rotor motor is the most common type in use
today as it requires simple control gear and, in most cases, can be used
instead of a wound rotor motor.
The bearings are used to support the shaft and to enable it to rotate.
You will remember the earlier reference to the rotating magnetic field
and how the rotor "chases" it. In theory, if there were just the one
magnetic 'pole", the rotor would rotate at a rate equal to twice the
frequency of the supply, that is to say, for a 50 hertz ( or 50 cycles per
second) supply the rotational speed would be 100 revolutions per second, or
6000 rpm.
In practice it is not possible to create one magnetic pole without at the
same time creating an equal and opposite pole, so the highest achievable
speed for an AC induction motor using a 50 HZ supply is 3000 rpm.
It is possible to arrange the stator windings in such formations as to
provide any number of PAIRS of poles and so we can offer 2,4,6,8,10,12 pole
motors etc. Motors over 12 pole are available if required but are not in
common use.
Poles and Synchronous Speed
No. of poles are determined by no. of magnet poles.
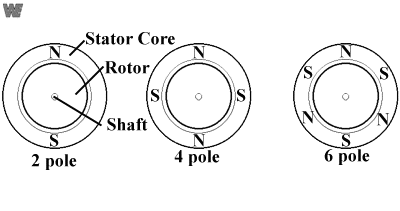
And they should be an even number.
Remember that as the number of poles increase, so the speed decreases.
We call the hypothetical speed "Synchronous" speed because it is the
speed that would be obtained if the rotor rotated in "Synchrony" with the
magnetic field. In any AC induction motor , the synchronous speed is never
achievable, since friction losses in the bearings, air resistance within the
motor and additional drag imposed by the load combine to cause the rotor to
lag slightly behind the rotational speed of the magnetic field. This lagging
effect is known as the "slip".
The "Synchronous" speed of a motor can be determined by the formulae:
Synchronous speed = 120 x f
Poles
where :
Speed is expressed in rpm
f equals frequency in HZ
and poles is an even number. (ie 2,4,6 etc)
If the frequency varies, the speed varies in a direct ratio.
The percentage slip varies from one motor to the next -- as a general
rule of thumb, the larger the motor, the less slip is experienced -- and for
any given motor the slip will decrease as the load decreases. At no- load
the slip may be as little as 0.5%, while at full load, depending on the size
of the motor, it can be high as 5.0%.
Thus typical "Full Load" speeds for , say , 2,4,6 and 8 pole motors, on
50 Hertz supply, could be 2950, 1470, 980 and 735 rpm respectively, compared
with the synchronous speeds of 3000; 1500; 1000 and 750 rpm.
It is not surprising to find that the "slip" of a motor is closely
related to the motor's efficiency, and in fact, the full load speed of a
motor is a good guide to the motor's efficiency.
The physical size of a motor is not purely dependent on the kW rating. A
15 kW 6 Pole motor, for instance is far larger than a 15 kw 2 pole machine.
If there were a single factor which determines the frame size of a motor
( and there isn't) it would be the torque. Torque is the rotational
equivalent of linear force and for any rotating machine, if the Power and
Speed are known then the Torque is given by the formula:-
Torque = kW x 9550 Newton Metres
rpm
When a motor is driving the load at full speed, the torque
developed by the motor will always equal the torque required by the load to
keep it running at that speed. The more accurate the motor selection, the
closer this torque value will approach the rated full load torque (F.L.T.)
of the motor
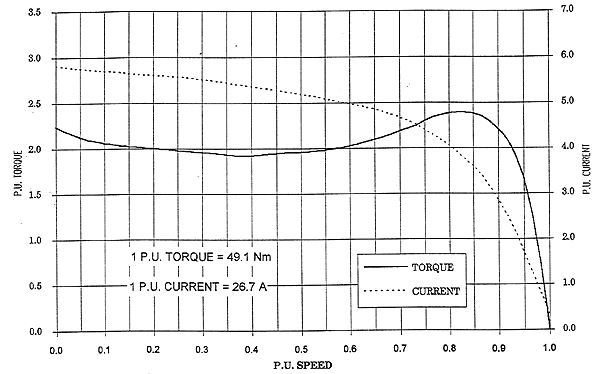
During the starting cycle ( or Run Up Time), however , the torque
developed by the motor at any given instant must always exceed the torque
required by the load at that particular speed, otherwise the load will not
continue to accelerate and the motor will stall.
At any given speed during run up, the difference between the motor torque
and the load torque is known as the Accelerating Torque and, taken over the
complete curve of torque against speed from zero to 100% speed, it is this
accelerating torque -- together with the load Moment of Inertia -- which
determines the run up time.
The above curve is typical for a squirrel cage motor.
The initial point is known as the Starting torque or locked rotor torque
(L.R.T.) , the minium point is known as the Pull Up torque (P.U.T.) and the
maximum point known as the Pull Out Torque (P.O.T.)
The above explanation is a very simplified explanation of "How a Motor
Works" but we hope it will be of some help to enable a "layman" to
understand.
The writer would like to acknowledge assistance from various articles and
technical papers in preparation.